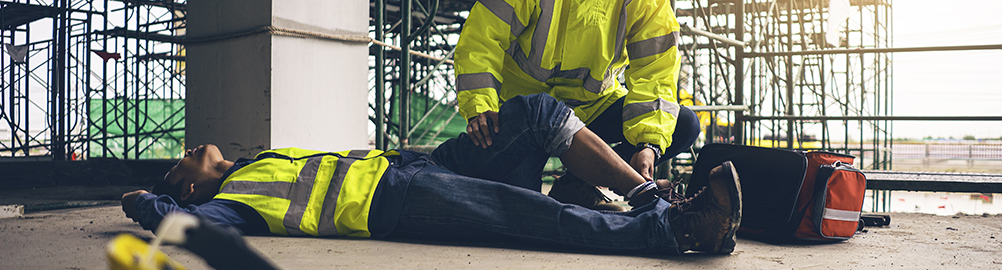
5 Most Common Workplace Injuries and How to Avoid Them
Safety Matters
According to the Association of Workers’ Compensation Boards of Canada, there were 1,027 work-related fatalities in 2018. In this most recent year reported, 665 of fatalities were due to occupational diseases, while 362 were caused by injuries. To put it another way, on average one Canadian worker loses their life at work every day. The total number of accidents is much higher when non-fatal injuries are counted, reaching 264,438 across all Canadian provinces and territories in 2018.
- The province with the most workplace injuries was Quebec (78,504).
- The province with the most fatal injuries was Alberta (86).
Compared with previous years, 2018 had higher rates of lost-time injuries and fatal injuries, indicating that Canadian workplaces are becoming more dangerous. However, many accidents can be prevented with the right knowledge and equipment. Online safety training is an excellent option to keep your collaborators updated with the latest safety regulations and technologies.
This article will discuss five common workplace injuries, with some effective recommendations to avoid them.
1) Sprains or Strains
These two terms describe similar injuries, and they are often used interchangeably. However, there is an important distinction between them:
- A sprain is an injury that affects ligaments, the tissue that connects bones with each other. Sprains occur when ligaments are torn or stretched too much.
- A strain is a similar injury since it also involves stretched or torn tissue. However, strains affect muscles or tendons, not ligaments.
These injuries are more likely to occur in situations where workers handle heavy materials or equipment and exert too much force. Employers can help prevent strains and sprains by modifying workplace practices, so workers don’t have to carry heavy objects across long distances. For example, filling buckets to a minimum height to ensure workers do not overexert themselves. Of course, companies should also ensure that lifting equipment and tools are in good working condition. Proper online training can also help workers avoid sprains and strains. Employees can take all the necessary precautions from the start if they can actively identify dangerous or strenuous situations.
2) Cuts and Punctures
There are many causes of cuts and punctures on worksites, but these injuries most often occur when sharp tools are not used properly. To reduce this type of injury, two measures are very effective:
- Training workers on how to use tools and equipment safely.
- Providing adequate personal protective equipment (PPE), and making sure it is used properly each time.
Many cuts and punctures are superficial and they only affect the skin. However, in severe cases, they may injure muscles, tendons, ligaments and even bones. These wounds should receive immediate medical attention since they can easily become infected. Untreated cuts and punctures can also cause tetanus, which is can be fatal.
3) Broken or Fractured Bones
Bones are often fractured as the result of a traumatic injury, such as falling from a ladder. However, microfractures can also develop from repetitive movements that exert a force on bones. As skeletal tissue deteriorates with age, companies that employ seniors must be especially careful since these employees are more vulnerable to breaking bones.
Like any workplace hazard, training can reduce the risk of suffering a bone fracture. The following are some recommended topics to cover:
- Fall protection
- Ladder safety
- Slips, trips and falls
- Safe use of equipment
- Working at height
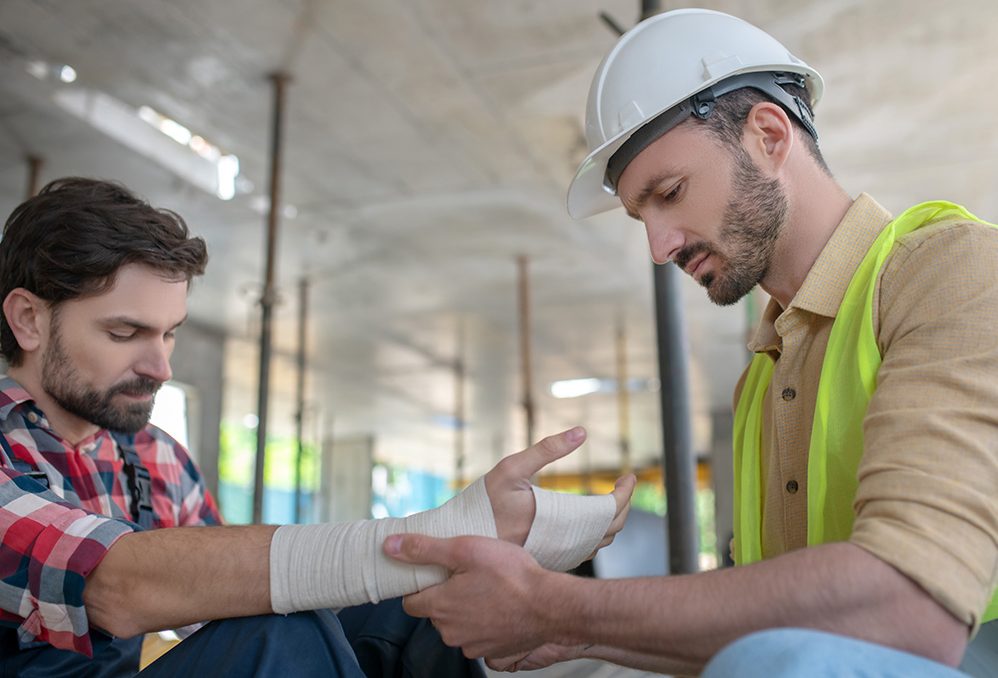
Bone fractures are very painful, and in extreme cases, they can cause long-term disability. Accident prevention is a part of being socially responsible, and it also contributes to a productive workforce.
4) Poisoning
Many substances found in workplaces are toxic, especially in industrial settings. Even when following common sense, there are many ways in which exposure can happen:
• Some toxic substances are gaseous, or they evaporate quickly. Workers may be intoxicated by inhalation.
• Accidental ingestion may also occur. For example, a hazardous liquid that is clear and odourless can be mistaken for drinking water.
Canada first published the Workplace Hazardous Materials Information System (WHMIS) in 1988, and the Globally Harmonized System (GHS) from the United Nations was adopted in 2015. Organizations should provide up-to-date WHMIS training for their workers to ensure that all hazardous product labels are clearly understood.
5) Burns, Scalds, or Chemical Burns
In addition to toxic substances, workplaces may also contain hot surfaces and liquids, or harmful chemicals. WHMIS training can also help prevent these accidents, by making workers aware of product labels and their meanings. Workers should use adequate PPE when there is a risk of burns, scalds or chemical burns while following safety protocols. For example, a container with an acidic chemical should not be handled unless it is properly closed and the appropriate PPE is worn.
Conclusion
Unfortunately, workplace injuries are common, and in some cases, fatal. However, companies can create safer workplaces by providing all the necessary information to their employees and all the tools and equipment needed for protection. Accident prevention starts with being aware of the hazards present, and this can be accomplished with online safety training. When employees are aware of the threats present in a work environment and are provided with the knowledge and tools to avoid them, the risk of a fatal injury is greatly reduced.