
9 Safety Metrics You Need to Track
According tothe AWCBC, 925 Canadian workers lost their lives on the job in 2019?
Regulatory bodies like the Canadian Centre for Occupational Health and Safety (CCOHS) and Occupational Safety and Health Administration (OSHA) have been doing a good job at increasing safety and reducing the current worker risks and accident statistics. However, they’re having trouble reducing death and injury rates past the threshold – which rests at a regular 2.8% over the past few years. It is crucial that all companies track safety metrics and consistently work to improve their overall employee well being. This will help reduce the number of accidents and fatalities.
Read on to learn about the 9 safety metrics you need to track.
1. Completed Safety Training and Employee Training Records
In many industries, employee safety training records are mandated to be kept for a certain period of time, and renewed with each new training session. Even if you are in an industry that does not mandate safety training records be kept in order to be in compliance, it is always a good idea. Maintaining accurate records can help you assess the efficiency of your employee training programs, get a stronger return on investment on your training method, and mitigate potential litigation.
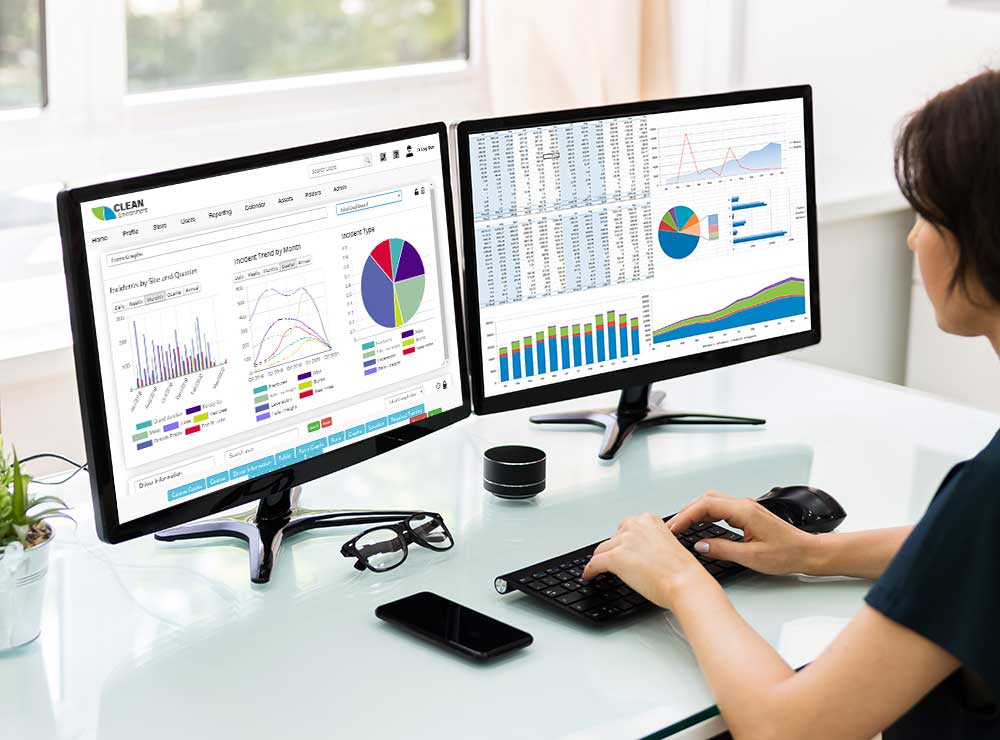
2. Expired Training Records and Certificates
To keep employees safe they need to be trained on proper safety procedures. As an employer or safety professional it is important that you keep ahead of expired training. Investing in this process regularly can also boost employee efficiency and improve the business overall.
3. Incidents and Near Misses
OHS authorities require employers to not only record this information, but also post it on the job site and keep it current throughout the year. For more information on how injuries are defined and classified, as well as to learn more about CCOHS statistics, you can visit their website.
4. Internal and External Audits
Workplace safety audits can occur at any time. Keeping track of these audits can assist in keeping your entire company safety-minded. They can also serve as recommendations for what can be improved upon, and potentially troubling areas of employee safety to watch out for. A consistent internal assessment of employee safety is strongly recommended, so you can be prepared and ensure you are training employees when they need it as well as being prepared for external audits.
5. Hazards Identified
Safety audits and daily field level hazard reports from employees will provide you with an updated list of hazards in the workplace. These hazards need to be addressed with your safety management system. The results of audits and daily reports can be distilled down into a hazard tracking system – giving you a clear and detailed picture of areas that are consistently risky when it comes to employee safety.
6. Operational status of equipment
This is a fundamental safety metric to track internally, providing you with the status of equipment in worksites and the shop on a regular basis. Well-maintained equipment helps keep employees safer. You can ensure that it meets the OHS regulations of your province or territory and that the machines are in good repair. Beyond serving an employee safety role, this step saves you money by showing you where to invest in regular equipment maintenance.
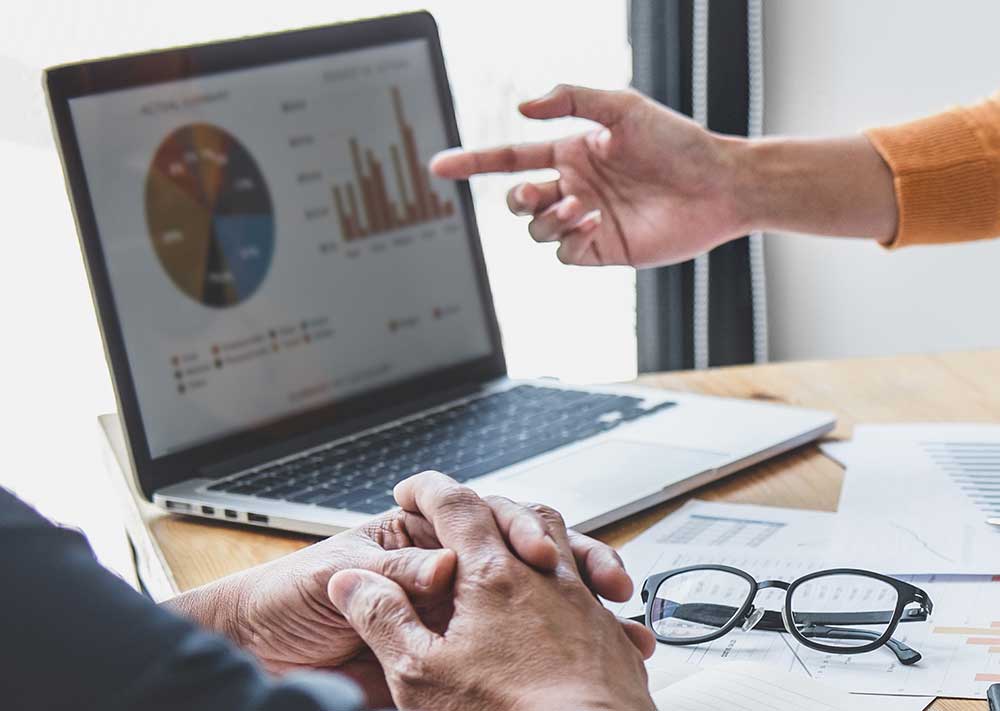
7. Lost Work Hours and Days
In order to improve your safety you need to be able to see if your numbers are improving or getting worse. One of the best indicators is lost time due to injury and illness.
Recording lost work hours and days due to employee injury and other accidents is required for reporting purposes. Regulations have changed their interpretation of this requirement over time, now becoming more inclusive and descriptive when counting days lost. For the most up to date information on how to count these days, you can check the CCOHS FAQ.
8. Tracking Toolbox Talks
A toolbox talk is anything that constitutes an formal safety meeting with employees in the workplace. Regulations don’t normally ask you to track these meetings, but you should – they can show you the general mindset toward workplace safety and the importance that your employees place on it.
Track how often they are occurring and employee attendance. It is possible to efficiently track this information if you use a safety software tool that includes toolbox talks.
9. Non-Compliance
This is a critical metric to track, since it tells you directly where your safety program is falling short. Supervisors and managers need to be recording non-compliance by your employees. This should be tracked with the goal of full compliance, and to help you see what changes should be made to reach your safety goals.
Safety in The Future
Tracking safety metrics goes far beyond what is mandated – a safety program that is constantly improved with data can go a long way in protecting your employees. This process can boost trust, morale, satisfaction, and well-being. Track these 9 key safety metrics today and begin reaping the rewards of a safer workplace!