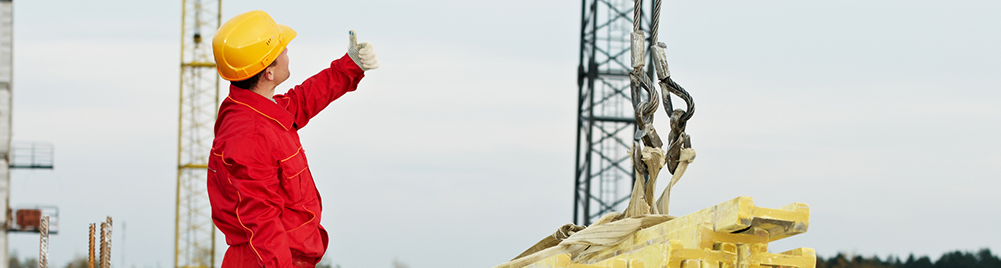
6 Safety Tips for Basic Rigging
Lifting operations are important in construction and other heavy industries, and they must be planned carefully to reduce the chance of accidents. A key step of the process is rigging, which consists of preparing the load for lifting equipment such as cranes or hoists.
Any workers who will participate in a lift must be trained on basic rigging safety. Even if the crane has enough capacity to lift the load, it can slip and fall without proper rigging. An accident like this can cause severe injuries, fatalities, and major property damage. Workers must have access to safety manuals and proper equipment to ensure that rigging is performed correctly.
Overview of Rigging Equipment
An entire course would be required to cover the topic of rigging in detail. However, the most important elements in many lifts are slings and hardware. How the slings are attached to the load is called a hitch and it is important to choose the proper one to avoid accidents. There are three main types of hitches, according to the Mechanical Contractors Association of America (MCAA):
- Vertical hitch: The sling attaches the load to the crane hook in a straight line.
- Choker hitch: The sling wraps around the load, with one end attached to the crane hook and the other end attached to the sling itself.
- Basket hitch: The sling also wraps around the load, but both ends are attached to the crane hook.
There is an additional type called the bridle hitch, which can be considered a variation of the vertical hitch. Instead of using one sling in a straight line between the load and crane hook, there are multiple slings and attachment points. In other words, the load is carried by several slings, but without circling the load like a choker or basket hitch.
There are many sling types for basic rigging, and also several types of hardware used for connections. The ideal types will depend on the load conditions, and the rigging team can improve safety with an adequate selection:
- Sling types: Synthetic round sling, synthetic web sling, wire rope and alloy steel chain.
- Hardware types: Hooks, shackles, eye bolts and wire rope clips.
All slings and hardware should get a proper inspection before every use to ensure that they can bear the load safely. In the case of slings, every inch of their length should be checked for damage before rigging. Hardware should be checked for signs of material damage, such as cracks or deformation.
Best Rigging Practices
1. Never work under suspended loads
There is still a chance that a load could fall, even if all the rigging safety procedures are followed. There is no reason to work under a suspended load, and any rigging adjustments should be carried out when the load rests on the ground. Once a load is being lifted between two points, the area below should also be kept clear during the operation.
2. Do not leave a suspended load unattended
A load should not be left suspended in the air without attention even with proper rigging since this creates several risks. For example, if a strong gust of wind moves the load sideways, the entire crane may lose balance and collapse. Weather conditions can change suddenly, and site personnel must be ready to respond.
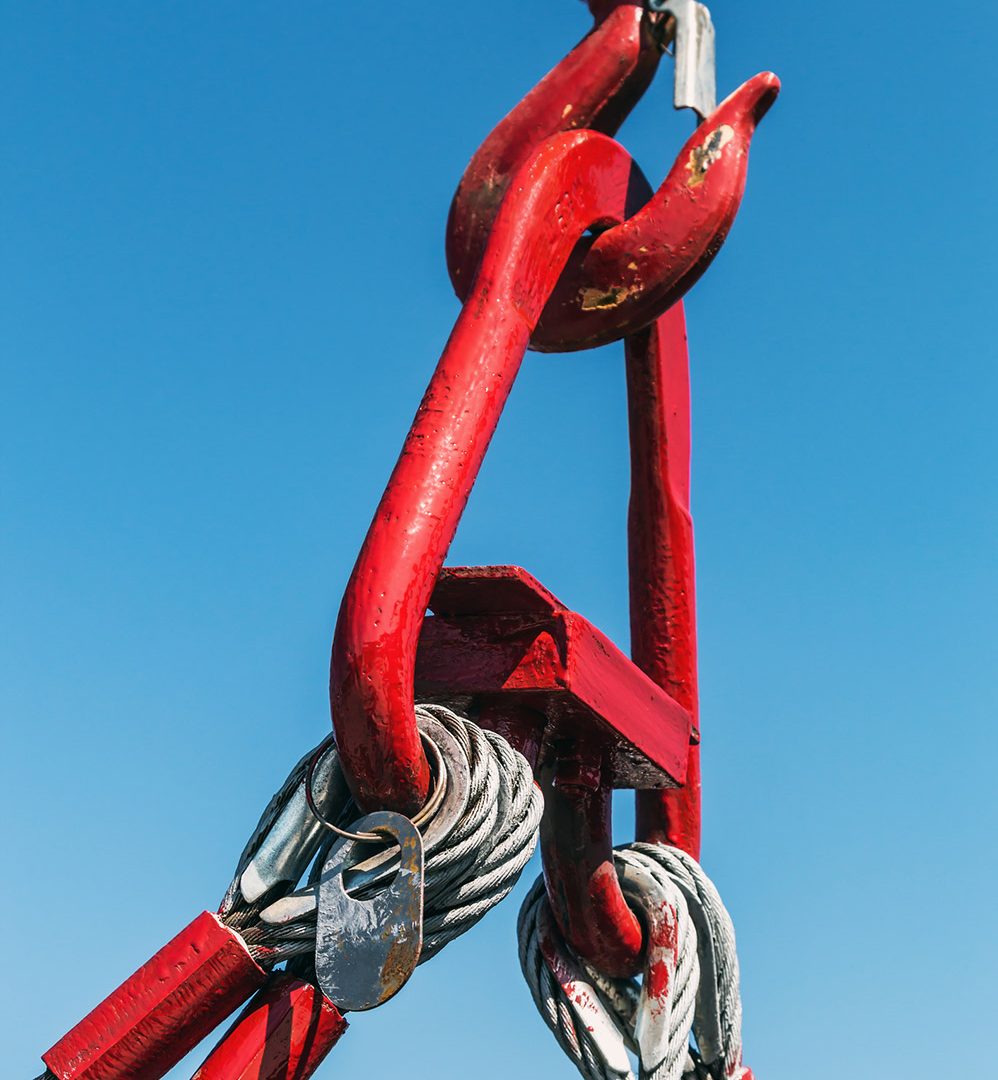
3. Make sure the load hook and suspension are in a straight line
The rated capacity of slings and hardware only applies when they are aligned vertically. In a bridle hitch, with multiple connection points, the slings and hooks are attached at an angle and their capacity must be derated. The capacity of hooks and other hardware is reduced as the load is displaced from its center.
4. Do not lift people with a hoist
Workers should only be lifted with equipment that is designed specifically for that purpose, such as mobile elevated work platforms. When a crane or hoist is used to lift a makeshift work platform, the risk of an accident is increased dramatically. For example, the platform can become unstable with simple movements by the workers. Weather risks also apply in this case, since a strong gust of wind can easily cause workers to lose their balance.
5. Make sure the load is balanced
When rigging is carried out properly, the load can be lifted without tipping or rotating. An unstable load can fall more easily, or it can even tip the entire crane. Since lifting equipment only exerts a tension force, it can be destabilized easily by a swinging load or a torsion force. Both of these forces can be produced by an unbalanced load. Marking the center of gravity of a load is useful for riggers and crane operators. Dangerous conditions are created when the center of gravity and the lifting force is not aligned.
6. Have a qualified spotter on site
An experienced spotter can prevent many accidents, by identifying risks before they materialize. For example, a qualified spotter can identify an unstable load as soon as the crane lifts it, and instruct the crew to place the load on the ground and adjust the rigging. A spotter can also communicate with the crane operator, indicating any hazards as the load is being moved.
Conclusion
Basic rigging safety is critical whenever a load must be lifted in a worksite. Even if the crane has the capacity to lift the load several times, it can be dropped due to inadequate rigging. Using the right slings, hardware and hitch for each load is critical to prevent accidents. This article provides an introduction to basic rigging, and it should not be viewed as a replacement for proper training. Qualified personnel is required in all workplaces that involve rigging, such as construction sites and shipyards. However, by being aware of the dangers of rigging, you can be a part of a safer job site.