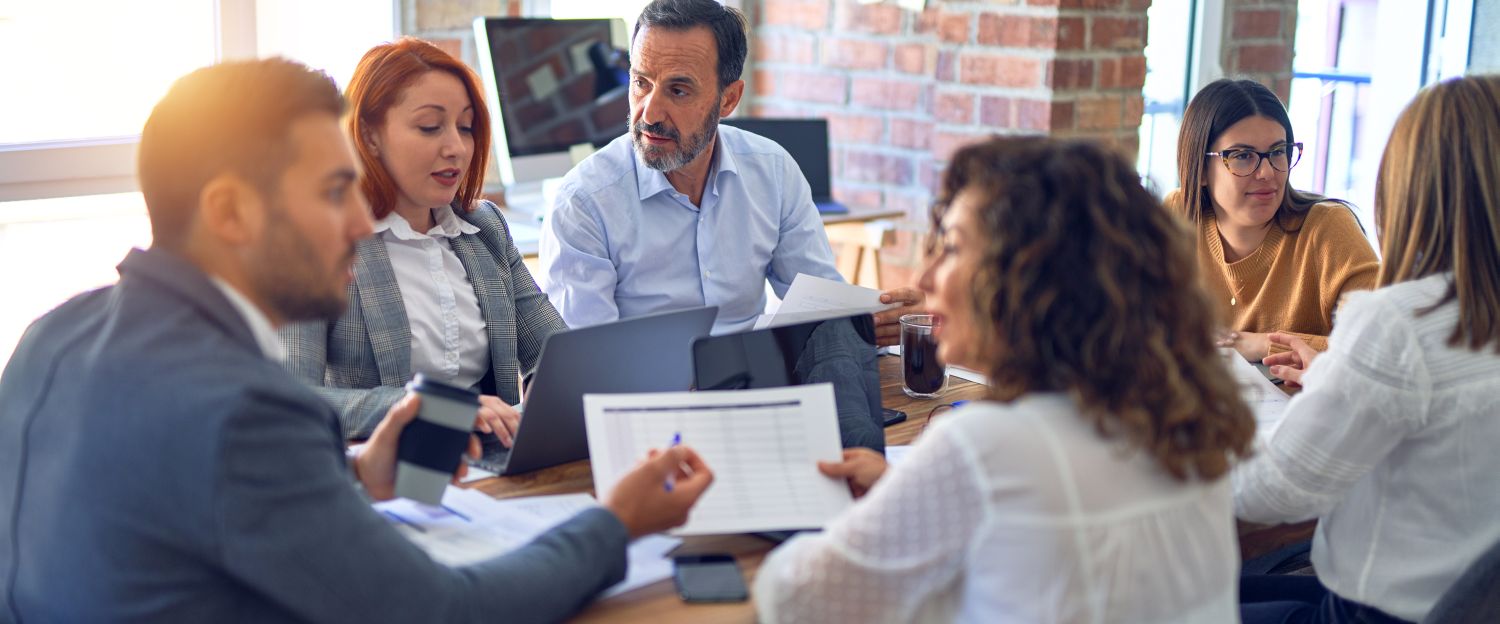
Getting the Most Out of Your Records
By Chontell Flight – Certified Health & Safety Consultant
If you’ve ever undergone a safety program (alternatively ISO, pre-qualification, DOT, FIOSA – audits, etc.) audit or otherwise formally assessed a safety program, you’d understand the importance of record-keeping – it is the #1 way to prove due diligence. When you record steps you’ve taken/what you’ve done, it is easier to reference these steps later on. This is why good record-keeping is so essential in roles like medical or policing, but no less critical in other roles at all workplace types.
In a recent JOHS Committee meeting I was asked by an employee ‘How many hazard ID’s are required to be submitted annually/monthly etc.?’ and it got me thinking that it’s a topic worthwhile exploring. The simple answer is ‘whenever you spot a hazard or experience an incident or near miss, record it’ but if we don’t continually communicate the message of reporting hazards, we are less likely to notice and identify hazards. As safety professionals, we’re familiar with the iceberg theory, and we know all too well that increased reporting may identify and allow for mitigation of risks before incidents are able to occur–‘nipping it in the bud’. But when we see significant incidents, or rising numbers of incidents, we know there are underlying unreported hazards lurking.
Documenting Like a Pro
"Good documentation starts with a great plan!"
My idea of a great starting point is a forms and records responsibility schedule. If your safety program doesn’t have one of these, it could gain you some additional points on that next audit, increase your compliance and outline expectations for records submission. There’s plenty of software that can assist in this process and when going this route, you can be sure to find it in times of need.
Some may disagree with my logic here, believing there should be a minimum requirement for numbers of records submitted. But what happens in those cases where we set arbitrary limits like ‘five hazard IDs due per month’? You end up getting a lot of repeat data, complaints, reports that are invalid (identifying non-hazards, jokes, etc.). Basically, the process isn’t respected in the same way. Sort of like a ‘boy who cried wolf’ scenario where the system winds up being largely ineffective.
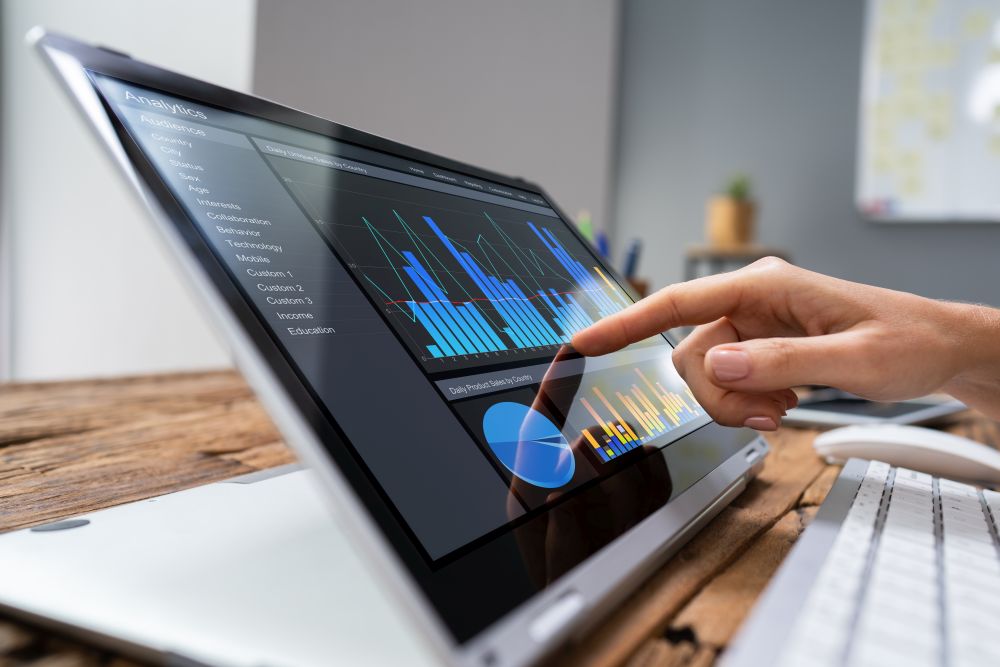
Instead, it’s better to continually use opportunities of communication with personnel to convey diverse types of workplace hazards and regular education on where they may exist in the workplace.
Some strategies for this include:
- At your Joint Health & Safety Committee meetings, toolbox, and other meetings where you have the ear of personnel, talk about seasonal hazards personnel may be expected to encounter (heat stress/cold stress, seasons of increased wildlife on roadways, icy/muddy conditions) to help keep them thinking continually about recognizing these risks. By fostering this sense of increased awareness toward hazard recognition, personnel feel knowledgeable and empowered enough to report (by record and/or to a supervisor) when they apply this hazard recognition to other workplace dangers. Risk awareness is something we must never grow tired of exercising, advancing, and building.
- Active listening is optimal. Grandmother always said ‘you have two ears and one mouth for a reason’ – and she wasn’t wrong! Active listening is so important – and when we listen with the intent to learn, we can hear real-time opportunities to help others identify and report opportunities for improvement, we absorb more information, and may enhance understanding. For example, a supervisor recently asked me how to complete a COVID-19 Risk Assessment Form that no longer reflected current regulations. I made note that the form required update since relaxed restrictions and vaccine requirements have changed compared to when the form was last changed. I affirmed that the personnel was correct and communicated that this could be considered a Hazard ID (albeit low) and that we could include the report as such. The corrective action required update of the form to reflect new hazard controls enacted allowing those vaccinated to be exempt from isolating after crossing the provincial border. Communicating this information has allowed the personnel to understand how this could be considered a hazard, how we can correct the error toward risk improvement, and reaffirm recordkeeping accuracy.
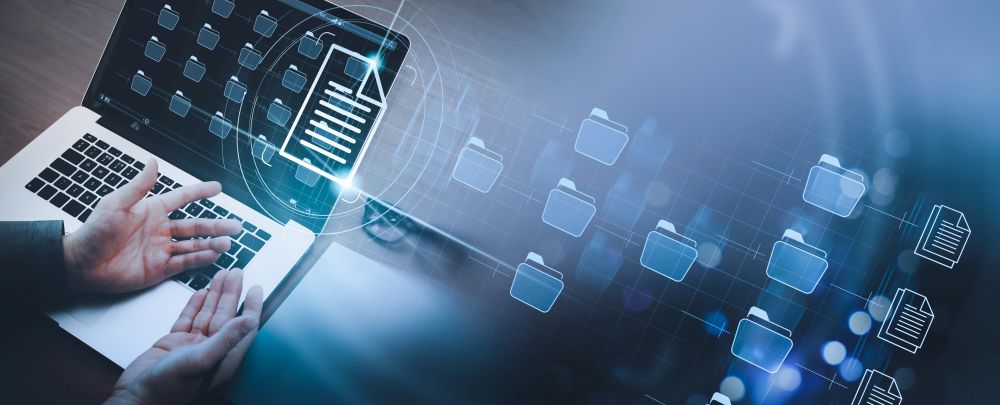
- Open communication and worker involvement is key. Creating a safe space where others feel comfortable sharing their concerns, thoughts and ideas allows for the best brainstorming and can help us see other perspectives. Including workers in formal hazard identification and assessment, participating in review of company safety statistics, or communicating concerns in safety meetings are all great opportunities for engagement and education. Simply put, people will participate where they are valued, heard, understood, and feel they are a contributing part of something bigger.
- Posters, signage, media, etc. We notice things that are new. Regularly (quarterly, monthly, etc.) change-up old hazard and risk identification signs at your workplace to catch workers attention in shared areas to keep them safety aware. Lots of free posters and signage are available through places online like the Canadian Centre for Occupational Health and Safety, through your local partnerships/workers compensation, and many other resources to keep everyone thinking safety first.
Functional Improvements
**Keep information on hazards current and draw attention to various types of risk**
Continually provide examples of what hazard IDs are in safety bulletins, safety meetings, etc. For example, when you are communicating quarterly safety statistics, you may want to include a note about the types of seasonal hazards that are upon us: i.e., whiteout conditions, slippery walking and driving surfaces, cold stress, dehydration, etc. When we continually provide examples of workplace hazards personnel are likely to encounter, they are more likely to spot and report similar or new hazards at the workplace-offering greater overall opportunities for improvement in risk reduction. This in turn helps instill a sense of value and input in the personnel to report those hazards and creates a supportive positive culture reflecting optimal health and safety participation and prevention.
So, for example, you may wish not to place a minimum or maximum number of records due for submission, simply make note quarterly of the hazard id/near miss, incident reports etc. received, and highlight other workplace hazards personnel should be aware of that are not identified in these records.
It’s also a good idea to include with your statistics why the company tracks and communicates those statistics with personnel. Conversely, if you set hard deadlines for submission, like ‘hazard IDs due weekly’, you are likely to instead get an overwhelming amount of repeat hazards, reporting of non-hazardous items to fill the requirements, and instead miss the reporting of new hazards-in short, a larger amount of non-usable information.
Instead, if the end of the quarter comes and there have been no hazard IDs received, we could explain some of the prevalent hazard’s workers are exposed to due to current work projects, seasonal hazards, new equipment, etc. to encourage reporting of those hazards. The JOHS Committee Meetings are also a great time to discuss workplace hazards.
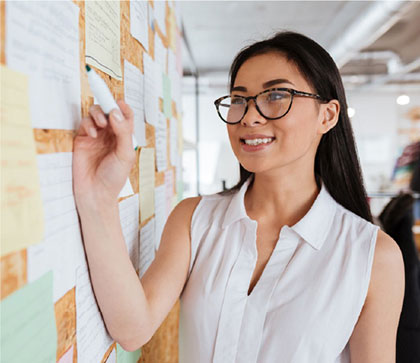
One of the greatest opportunities to share information with personnel and score brownie points on your compliance is with quarterly and annual statistical reporting. These quarterly information bulletins reviewed with personnel may reflect distinct types of company information like:
- Number of incidents, hazard IDs and near miss’, medical aid, lost time, etc. (while you may want to leave out specific incident investigation information for privacy reasons, it’s important to explain what happened, contributing factors, identify root cause, likelihood of recurrence, and corrective actions taken to implement hazard controls or process/equipment/other changes.)
- Hours of worker exposure
- Kilometers driven
And other information which you may deem relevant or as required by other systems (pre-qualification or quality systems for example, may have other data requirements).
TIP: I highly recommend when updating your company’s formal hazard assessments in the safety manuals/safety programs etc. that you consider a review of previous incidents/hazard id/near miss to see what, if any, can be included in your formal risk assessment updates to ensure all identified hazards are formally evaluated for effective risk management.
What a great way to demonstrate personnel participation in development of formal hazard assessments + competency of hazard identification and reporting all at once!
What to do if you do not have any incidents or hazards to review in your statistics?
Try reviewing industry-related incidents, or other incident in the media that may apply to your workplace or tasks. Incidents that happened at other companies or competitors. Learning by reviewing past incidents is the smartest way to learn and it’s important to soak up all that information. The key is to get people thinking about safety-it’s the wheel we want to keep greased!
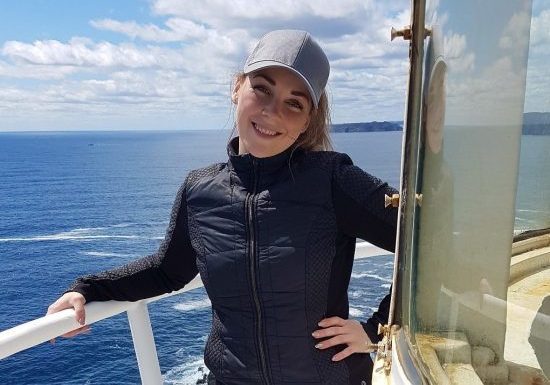
Chontell is a Certified Health & Safety Consultant at Rock Solid Safety Solutions with 10 years of industry experience and COR auditing expertise.
Safety blogger & self-proclaimed safety nerd.
‘My goal is to foster interest in safety management using innovative and creative solutions to reduce risk and refine systems. To encourage and motivate personnel toward successful involvement in safety program customization, team building, and promoting a positive safety culture. I believe all people can offer constructive contributions toward safety management for the greater good.’