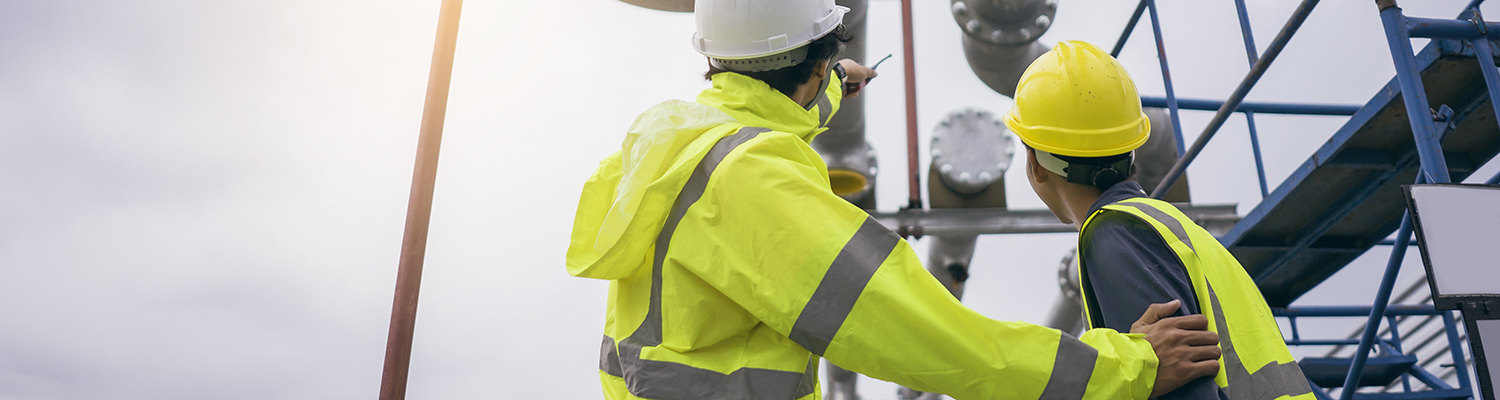
Reducing Incidents in the Workplace
Incident Management Systems for Reducing Incidents
Let’s face it; incidents at work are bound to happen, and when they do, they are disruptive and costly. The loss of equipment or infrastructure to an incident can lead to expensive repairs and downtime, emphasizing the need to stop workplace incidents before they happen. Equipment is one thing; accidents in the workplace that result in employee injuries (or worse, fatalities) will have an even larger effect on an organization.
It’s easy to understand why there is an increasing acceptance of safety procedures and policies, and why google searches on workplace safety receive so much traffic.
There is good news, however. With some foresight and planning, it is possible to keep your workplace incidents under control. And it all starts with devising a plan. This article covers the main points you should consider when reviewing or implementing safety practices in your organization.
Create a Safety Culture
It sounds like one of those kitschy sayings you hear CEO’s reciting at press conferences, but the reality is that if you want your organization to be safe, you must embrace the idea from top to bottom. What does that mean?
Safety requires a buy-in from all levels in your organization, starting at the top. You need to engage management and employees when creating your safety policies, and it works best when the highest levels of leadership are setting examples for the rest of the staff to follow. A supervisor or operations manager walking through a worksite without the proper PPE does not model good safety behaviours.
Talk to employees. Talk to management. Engage staff at all levels. Find out all their struggles and concerns. When you make everyone a part of the solution, you’ll find they will be more willing to cooperate.
Analyze your Organizational Hazards
You may need to seek help for this stage. After doing your job for a while, it’s easy to overlook common areas of occurrence, so bringing in a fresh set of eyes – specifically eyes that are trained to identify safety risks – will help you find the potential dangers.
Another way to tackle this problem is to review your past incident reports and see if you can identify trends. If you have multiple injuries due to slips in a specific area, perhaps the solution is as simple as replacing the flooring or putting up signs warning of slippery conditions.
Identify reoccurring incidents, but don’t overlook areas with fewer numbers either. Near miss reporting can help identify significant risks that haven’t happened yet. Good safety record keeping will identify trends within your organization; using an Incident Management software program will make this even better.
Develop Health and Safety Policies and Procedures
Some occupational health and safety policies are obvious. Hard hats and steel toes on a construction site, for example. Other policies may be less obvious, such as strategies to manage worksite stress or improving on-the-job communication. Doing your research is essential at this stage to understand all the potential risk areas within your organization, and how to properly develop policies and procedures to deal with them.
Depending on your skillset and your organization, you may need to hire an expert to help with this. Or, if you have lots of experience or are the DIY type, you will find a lot of information through online searches, and with some effort and determination, you can put together a solid safety program. A good system will include regular inspections and assessments, consistent communication between staff, stellar record keeping, and a commitment to see the program succeed.
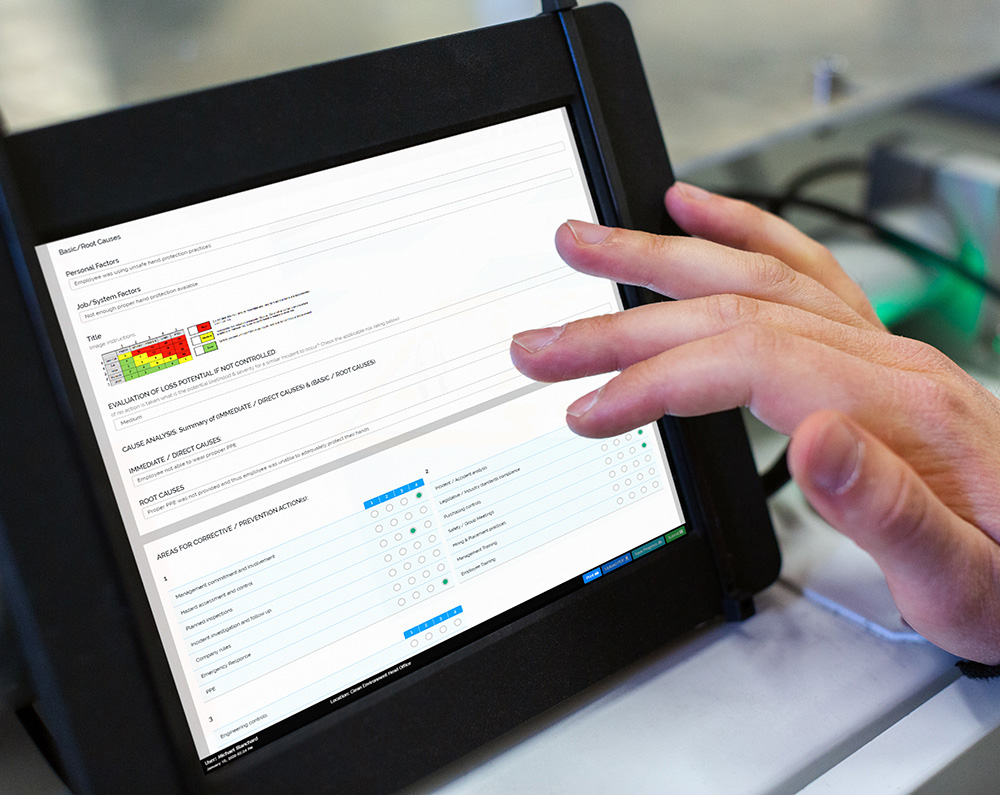
The most important thing is that you start. As you will see in the following steps, a good safety plan includes continuous review and updating. Develop a plan now, and then continue to improve it over time. As the saying goes, the journey of a thousand miles starts with a single step.
Leadership and Safety Training
It should not come as a surprise that training is a vital component to incident reduction. With common hazards identified and policies and procedures developed, ensuring your staff are properly equipped to navigate the workplace safely cannot be overlooked.
There are many options for training, and both classroom and online options can work well. Developing your own safety programs with the help of a learning management system is a great way to ensure your safety training includes the exact information your employees require, though it takes time and resources to create. Safety training partners can be a great resource to provide the training for you.
For a flexible option, look for a software solution that includes safety training courses as well as the safety management system to keep your organization out of the infirmary. The ability to track training across the entire organization with the use of a training record management system and a training matrix can help keep your safety program on track.
Learn from Experience
One last component to consider when devising a plan to reduce incidents in the workplace is to continually review the past. Looking over your incident history is a great way to identify trends for the things you are doing well, and the areas you need to improve. Has a training program helped to reduce a specific type of injury? Have incidents been reduced since mandatory toolbox talks were introduced? Ask lots of questions and look to your records to find the answers.
There are great software programs out there that will help with both the record keeping and the trend analysis. What’s most important is how you use this knowledge to continually improve your systems.
Keeping Incidents Out of the Workplace
We started by saying that incidents in the workplace are inevitable, and that may well be the case. But it’s also true that with a dedicated approach to safety best practices, the occurrence of incidents and accidents can be greatly reduced. Which should be the goal, year over year, for every organization – finding betters ways to be safe and reduce incidents every single day.
Let’s put on our safety goggles, tie up our shoelaces, and get to work.