Effective Safety Cultures
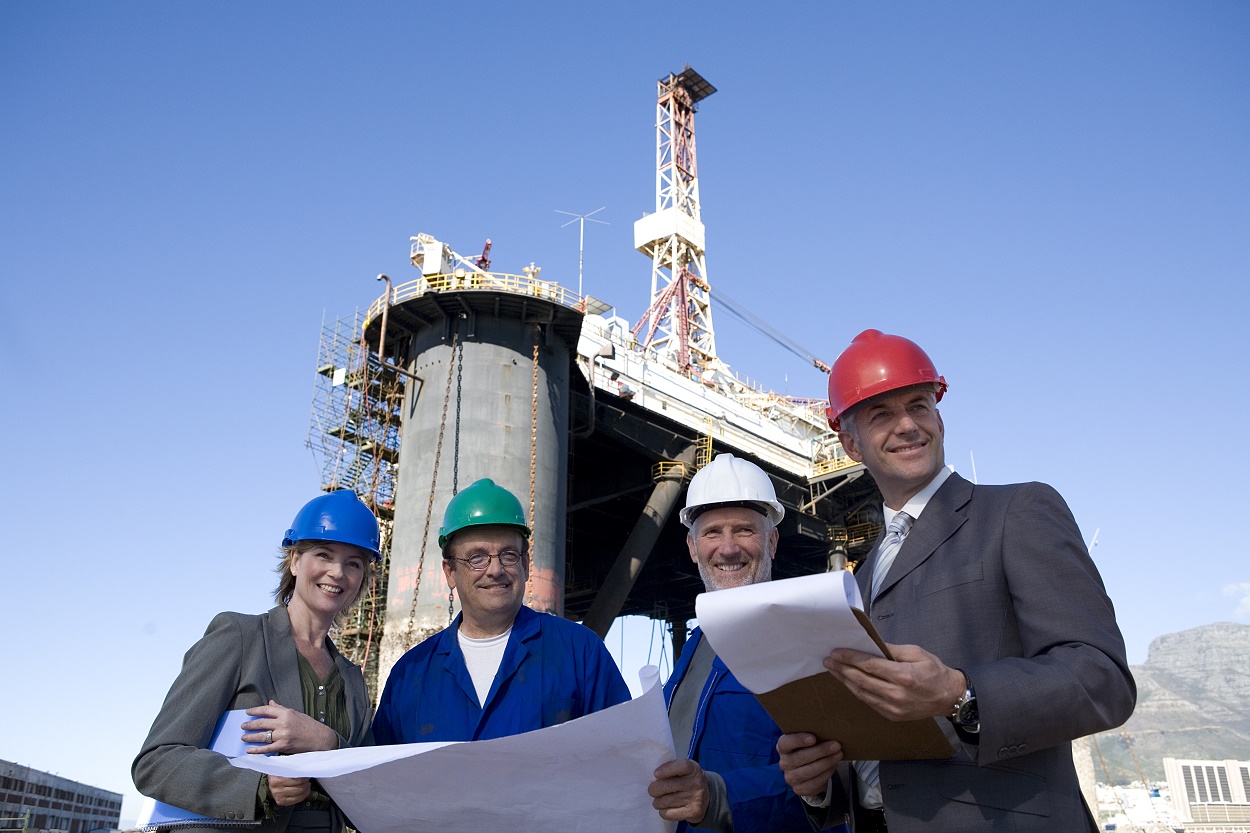
Establishing an effective safety culture means creating a shared set of values, beliefs, and norms around safety that management and workers alike can support and cultivate. That also means that establishing a culture of safety within any organization is a complex and difficult process. Once properly in place, however, it can be a powerful motivator that leads to big payoffs, a groundwork for further corporate culture, and an attitude rooted in long-term excellence.
The growth of an effective safety culture is scientific, with stages and benchmarks for success. It occurs through the careful analysis of work objectives, accident reporting, and scientific process. In an age where competitive edge hinges on the pruning of internal procedure, we must use behaviour modification to bring everyone to a collective agreement on what safety looks like before we can expect an increase in efficiency.
This process stems from the realignment of motivation. When safety programs wither, it is usually because the culture that currently exists aligns motivation with profit, not employee safety. To correctly realign employee motivation, managers must carefully select rewards and ensure they are built around scientifically selected objectives. With proper analysis, employee feedback, and communication, members at every level of the organization will start to propagate an attitude of safety excellence. As culture spreads, this becomes the prevalent way of thinking.
Safety Culture Assessment
In every organization, a culture already exists. Whether it is rooted in production, shared pastimes, or even negative behaviours like gossip, it is important to recognize and evaluate its source in order to alter its focus. The end goal is to guide the company by rooting new thought patterns and core philosophies in safety, and this requires research, analysis, and assessment.
The first stage of creating an effective safety culture is the analysis of current safety conditions:
- What sort of safety structure already exists?
- What level of communication currently exists around safety culture?
- Are standards for injury and incident prevention being met?
- Are current standards enough?
The decline of safety within an organization can be compared to an ecosystem losing balance—by the time numbers have visibly begun to shift, the cause of the problem already has a firm root. At this point, change is difficult. If incidents and injuries have begun to occur, poor attitudes and behaviour have already become commonplace. We must observe and analyze to determine what causes these poor attitudes and behaviours before we can begin weeding them out.
Questions about where to begin or which safety measures to implement are difficult but necessary during assessment. Asking these questions forms a natural foundation for the growth of a system that encourages leadership and accountability. Although it may be tough to measure and locate, probing employee motivation and the causes of unsafe behaviour slowly reveals the groundwork necessary for incident reduction.
Employee motivation and behaviour is important, but it’s just as important to evaluate management. What’s the real message behind company directives? Is it safety or production? Do behaviours or internal policies amongst management cultivate a “do as I say, not as I do” culture? Without proper research into current conditions, organizations can over-invest time and resources into the wrong sources of unsafe behaviour, causing more harm than good.
Therefore, determining where behaviour modification is necessary requires analyzing:
- Training
- Everyday work procedures
- Links to injury or incident statistics
- Time and resource investments
When analyzing, ensure you go beyond end-of-process injury statistics and examine behavioural statistics like near-misses and meeting attendance.