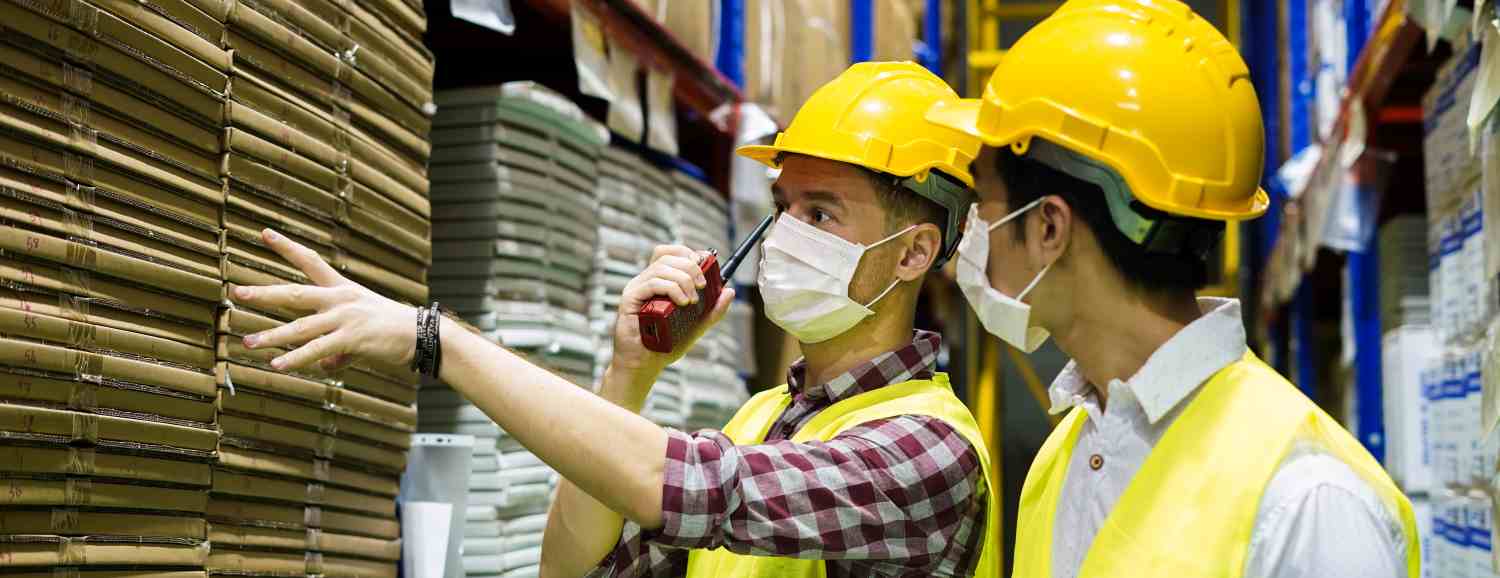
The Importance of Proper Workplace Inspections
Workplace inspections are important for many different reasons. When workers see a company putting in the effort to inspect a workplace frequently, it increases the awareness and presence of a safety positive culture, as well as signifies a company cares about the well being of its workers. Involving workers in inspections increases their participation and desire to also remain safe in their work as well as help keep their coworkers safe. Companies that put effort into conducting workplace inspections and implementing solutions to hazards are the most successful at keeping workers engaged, and safe in their daily work.
Safety inspections should be designed to look for workplace hazards that could harm a worker. Workers completing the inspections should have a good idea of what they are looking for prior to completing the observations of the inspection. Workplace inspections will not be very effective if the individual(s) performing the inspections are not trained on what to look for during the inspection. Different inspectors should be implemented so different eyes can observe the workplace and its hazards. Inspectors should not be inspecting their own areas as bias can exist, so rotating inspectors to other work areas is the most favorable. Involving workers in the inspection, permits another perspective to the inspections.
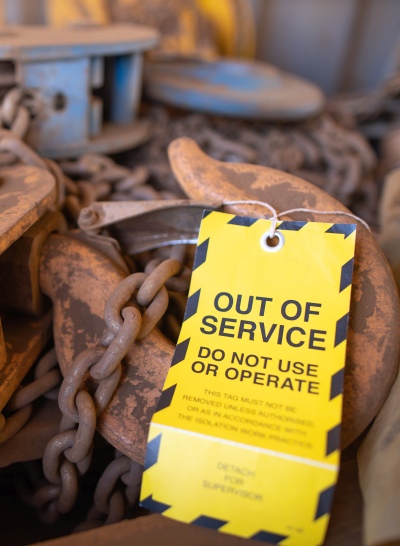
Safety committees provide another opportunity for workers to be involved in a company’s safety initiatives such as workplace inspections. A company should rely on its safety committee members to be willing to actively participate in workplace inspections where they can help identify hazards and come up with best solutions. Safety committee members should be trained in how to conduct workplace safety inspections which can help them best identify hazards. Safety committee members can also be relied on when debriefing from a workplace inspection. Involving more people in coming up with hazard solutions creates a better opportunity to come up with more solutions that can be implemented into the workplace.
Workplace inspections are not limited to just looking for hazards, they also include investigations of when hazards are reported and when incidents occur such as injuries or accidents. The investigation process of an incident should be thorough and all facts of the incident should be recorded when performing an investigation so all of the facts can be assessed and a root cause can be determined.
Just like other workplace inspections, it is important that the individuals involved in incident investigation have workplace investigations training. Proper training allows individuals involved in the investigation process to avoid biases when finding root causes, as well as implement the most effective solutions that prevent future occurrences of incidents that are investigated.
Organizations that are able to effectively determine root causes of investigations can implement best practices into the workplace that benefit its workers and help keep them safe at work. Root causes should also be investigated when a hazard in the workplace inspection is observed. Although an injury or incident may not have occurred from an observed hazard during an inspection, it could be likely to cause a future incident. Finding the source of the hazard and determining where it originated from, help guide the process of identifying safer solutions or approaches to the hazard that exists. Common root causes of hazards or incidents often lead back to gaps in training, poor work area design, a lack of commitment to safety from management, and human error. Establishing a positive safety culture can usually overcome most of the common root cause types.
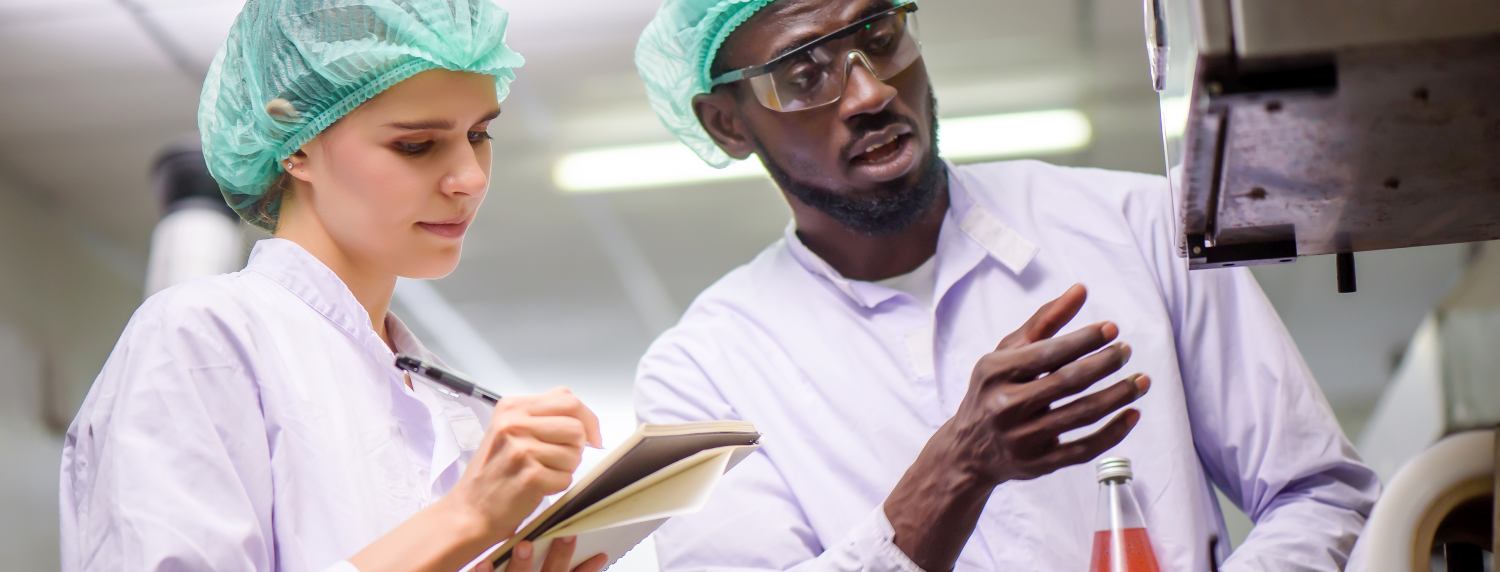
The final, and arguably most important aspect of the workplace inspection is to communicate the findings of the inspection as well as communicating what the planned solutions are for the observed hazards. Communicating the final outcomes of investigations and inspections allows the workforce to be informed of the organization’s actions. An informed workforce tends to participate more in helping find solutions to safety issues or concerns and also informs management of hazards in their work areas before incidents or injuries occur. Providing clear and understandable communications creates a workforce that understands the actions of the company. Communications should be carefully considered before issuing, because an overload of communications will overwhelm a workforce and learning may not occur as intended. Direct communications with intent behind the meaning are the most effective and should be favored when delivering.
Inspections and investigation are useless if action is not taken based upon the findings. Management must be committed to providing solutions to observed or reported hazards and should involve workers in finding the best solutions. Positive safety cultures include both proactive approaches by performing workplace inspections that detect hazards before incidents occur, as well as reactive approaches by performing detailed incident investigation that produce lasting solutions to prevent future incidents. A company that only focuses its efforts on one of the approaches over the other, is likely to find struggles and failures within their approach on safety when attempting to build their safety culture.