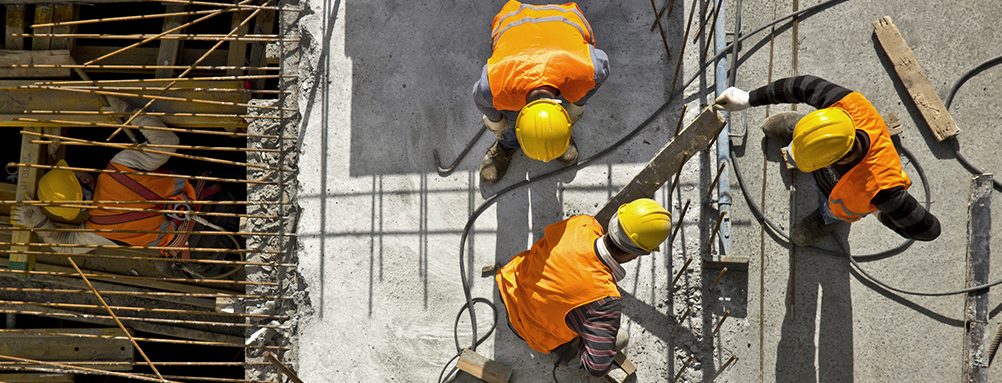
Tips to Improve Worksite Safety
Accidents can affect anyone in a company, and their legal and financial consequences can be severe. For this reason, worksite safety should be a top priority for all businesses. Providing a safe work environment is part of being socially responsible, but there are also financial reasons to invest in safety.
The Association of Workers’ Compensation Boards of Canada (AWCBC) publishes annual statistics on worksite safety. Their latest data covers 2018, and showed a total of 264,438 lost time claims due to work-related injury or disease, and 1,027 fatalities. The human consequences of an accident cannot be described in monetary value, but many organizations have analyzed the costs and benefits of workplace safety:
- In the UK, the University of Wolverhampton found that every £1 invested in accident prevention yields £3 in avoided costs.
- According to the US National Safety Council, 60% of CFOs report benefits of more than US$2 for every US$1 invested in injury prevention.
- The European Commission estimated that accident prevention has a benefit-cost ratio that ranges from 1.21 to 2.18.
Worksite safety measures protect the health and lives of employees while offering an attractive return on investment. However, safety requires education and adequate resources. This article will provide several tips on how to improve safety in workplaces.
Tip #1: Make It Your Top Priority
Worksite safety requires full commitment from a company since everyone is exposed to risks. Prevention measures have the goal of avoiding negative consequences. The time and funds used for accident prevention may seem like a waste when nothing happens, but that is the exact purpose of prevention. If a task or project is completed without accidents, the safety measures were successful. Safety measures may seem unavoidable expenses when only their costs are considered. However, when these costs are weighed against the accidents prevented, they become an investment. The same applies to time: safety measures can make some procedures slower, but a lot more time would be lost if an accident occurs.
Tip #2: Ensure Daily Safety Meetings
Workplace safety is an ongoing responsibility, and for this reason, it needs daily attention. Safety managers must ensure that all materials and resources needed for prevention are available. Daily meetings are important; they serve as a reminder under normal conditions, and they offer an opportunity to discuss risks that are only present during certain activities. Like any business process, safety involves completing documents such as Field Level Hazard Assessments (FLHA), daily inspections, or toolbox talks. This aspect of safety management is simplified greatly with digital forms since there is no need to carry printed documents and information is secured immediately. For instance, if a piece of equipment must be inspected daily, a digital form provides quick updates for safety managers. A printed form may delay the notification if a malfunction is detected. Someone may use the equipment and cause an accident before safety managers can give instructions.
Tip #3: Proper Personal Protective Equipment
Using personal protective equipment (PPE) is required on most job sites. In heavy industries like manufacturing and construction, the minimum requirements often include safety glasses, high-visibility vests, hard hats, and steel toe boots. In response to the COVID-19 pandemic, face coverings have also been added to this list. Additional PPE may be required depending on the work activity. Some examples of this PPE are welding helmets, fall protection harnesses and earplugs. Ensuring your employees have the proper training on PPE and have access to the appropriate equipment will protect them from hazards and keep them safe.
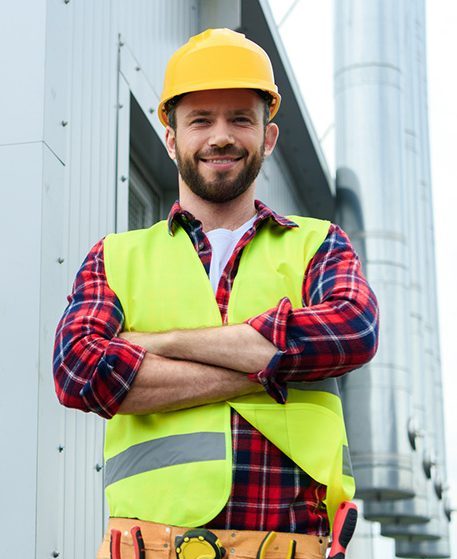
Tip #4: Train Your Staff
Safety procedures and PPE are much more effective when the staff has been trained properly. No amount of knowledge is too much when dealing with safety, and companies must also make sure their safety knowledge is up to date. Safety training is key for new personnel, but also when an employee is given a new responsibility or promoted. This also applies when the staff must get familiarized with a new procedure or technology, which may bring additional risks.
Tip #5: Create a Culture of Safety
Ideally, worksite safety should become part of the company culture. Once this is achieved, the staff will approach all tasks and projects with a safety-first mindset, even without specific instructions. In high-risk industries, a solid track record of workplace safety can also give companies a competitive advantage. A culture of safety requires ongoing training and having the necessary resources for prevention at all times.
Tip #6: Keep Everyone Accountable
Since anyone in a company can cause an accident, all employees should be accountable for worksite safety. Involving only the management staff is a mistake since they don’t interact with risks as frequently as technical personnel. Safety management is simplified when everyone is involved, and this includes data collection for audits and inspections. When the entire company is involved in worksite safety, everyone becomes a potential safety auditor. This means any employee can verify if people are following safety protocols.
Conclusion
Worksite safety should be a priority for companies, since protecting employees is a part of business ethics. Several studies have concluded that safety investments have a much lower cost than the accidents they prevent. From a business perspective, safety can be considered a lucrative investment. Companies should provide enough materials and adequate training to make workplaces as safe as possible. At the same time, safety should be promoted with daily meetings and by involving the entire company. Worksite safety is an ongoing responsibility, and it should not be viewed as only a checklist with requirements. These tips should be used to help create a safe and efficient work site for your employees and team members.