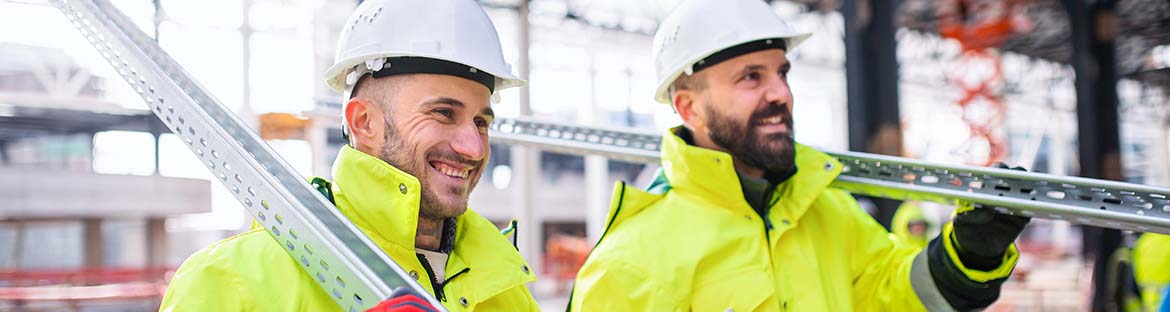
Top Lessons from Some of the Safest Companies
Lessons From the Safest Companies
According to a 2019 report from the US Bureau of Labor Statistics, the number of fatal workplace accidents has plateaued at roughly 3.5 fatal injuries per 100,000 full-time workers. This number has held fairly stable from 2010 to 2019. Everyone would agree that we want to continue to decrease the number of workplace accidents across Canada, the United States, and the rest of the world. To break the plateau and start decreasing the number of fatal accidents it would benefit us all to look toward the safest companies across the world and see what they are doing well and put these lessons to work within our own organizations.
We have found some of the top lessons learned at the world’s safest companies and included the most actionable into a list for you to put into practice at your company. Hopefully, together we can all improve workplace safety and reduce the number of incidents, especially those that are fatal.
Top lessons from some of the world’s safest companies include:
1. Only Hire People Who Truly Value Safety
Everyone within your organization must value safety above all else. If this is not the case, you must make some personnel decisions and remove those that do not share these values.
When hiring new workers, whether full time or contract, you must ask questions that get to the root of their philosophy on safety. Try to decipher how they truly feel about safety. Will they put speed ahead of their safety? Will they put speed ahead of the safety of their colleagues? If they are willing to do either of these then you need to continue your search for another employee.
As a growing company, rushing to fill positions and skipping the thorough interview process is a mistake. Having a single person join the team who does not value safety above all else, will quickly erode the culture of safety that you are trying to establish within your company.
2. Create a Culture of Transparency and Honesty
Creating a safer company starts with being honest with your employees as well as the outside world. Some companies hide safety or incident data from their teams and from the public but being completely transparent creates an atmosphere of trust which can actually encourage your team to work harder for you and build a stronger culture.
It is hard for your employees to grasp the effects of their actions, whether safe or unsafe, if they are not seeing how it impacts the safety trends at your company. It would be tough to expect an employee at worksite A to learn from the mistakes of employees at worksite B if the information is not shared openly.
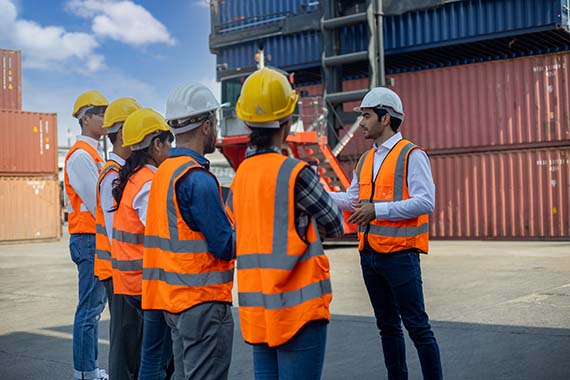
3. Hold Regular Safety Meetings with Leadership and Workers
One of the most common practices among the safest companies is their habit of holding regularsafety meetings whether incidents have occurred or not.
Some companies put off regular safety meetings until a major accident occurs, but that is most definitely the wrong time to be holding these meetings. Actually, let me take that back, holding meetings after an incident is critical to assess and debrief to try to prevent a similar incident, but holding regular safety meetings, and involving leadership in these meetings, can help PREVENT the major accidents from occurring in the first place which is obviously a better outcome.
4. Empower Workers to Make Safety Decisions
The safest companies empower their employees to make good decisions for the best safety outcomes even if it means sometimes, you must bend or break a rule. Most companies will set rules and best practices with the best of intentions, but occasionally they will overlook various scenarios that could cause major issues. Employees need to be given the space and freedom to think for themselves and analyze situations as they come up will help prevent accidents caused by following rules for a rules sake.
5. Track Data Related to Company Safety
In our first tip, we talked about being transparent with safety data, well to do that, first, you must have the data to share.
If you are not currently tracking safety metrics, setting goals, and measuring your goal achievement then you are missing a critical part of your safety program. You need to be able to see the data to be able to view trends because quite often what we believe is a trend could be incorrect and we could simply miss a startling pattern because we are not tracking the numbers.
6. Always Build Out Your Safety Plans Based on the Strictest Region
Many of the safest companies have multiple worksites and locations across the countries within which they operate. These companies will often take their safety policies from the most regulated areas and apply them to all their business units rather than having different standards in different locations.
Not only does this provide consistency and allow workers to easily transition between worksites without confusion about safety, but it also takes the learning and practices from the safest areas and applies them to others whether the government has mandated it or not.
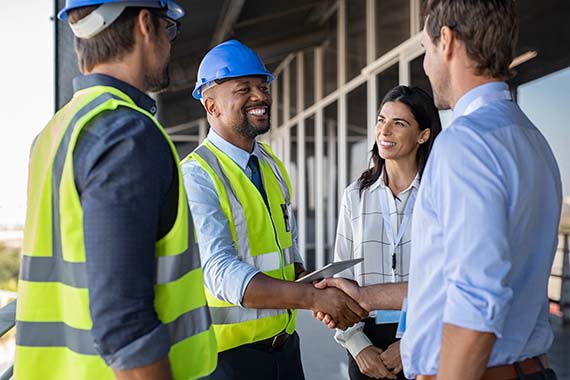
7. Tie Supervisor/Management Bonuses To Safety
Even if a supervisor or manager is not in a specific safety role like EHS Manager or OHS Manager, some part of their performance review or bonus should still be tied to safety outcomes within their department or business unit. Creating this safety connection to every supervisor and management role within your organization will help motivate the upper levels of the company to take safety seriously even if they have relatively low-risk roles themselves.
So How Can I Be Safer?
The safest companies in the world share many of the same best practices. Taking these teachings and bringing them into the fold at your organization, when it makes sense to do so, can help us all break the safety plateau. If we pay attention to the success of others, we can all start dropping the rates of workplace injury and death even further, and at the end of the day, that is all that matters.