The science behind human behaviour
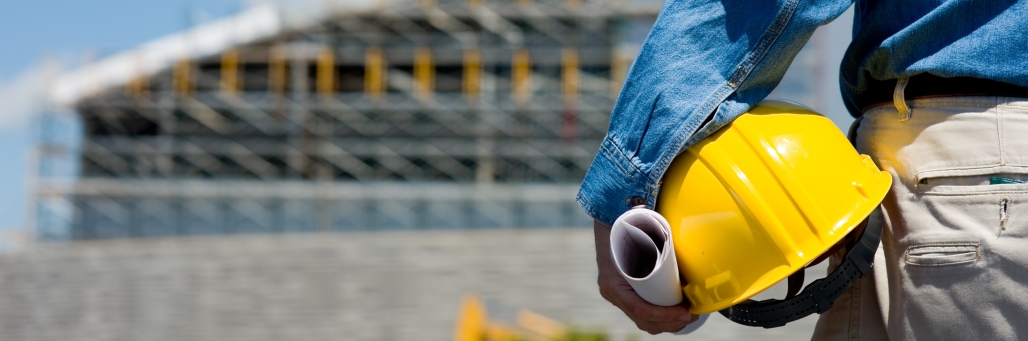
Behaviour-Based Safety
Behavior-Based Safety (BBS) is the process that creates a safety partnership between management and workers, focuses on people’s behaviour related to how they work, and encourages all workers to be safe and to work safely all times. Behaviour-based safety (BBS) has become increasingly popular since Frederick Taylor first pioneered scientific production management in the early 20th century. Today, his basic principles of standardized procedure and interdepartmental cooperation still steer the processes behind increased efficiency and systemized safety for many corporations.
BBS is based on the principle that unsafe work behaviours are responsible for the majority of workplace incidents and reduced productivity. By identifying, measuring, and correcting critical behaviours, management is able to produce the desired safety and production statistics. One key way that we can reverse unsafe behaviour patterns is by developing a system of positive acknowledgment and reward that motivates employees to engage in safe practices.
This process begins with the scientific study of behaviour through identification and analysis, followed by continuous observation to determine the potential causes of unsafe work. Then, by applying what we know about the science of individual and group motivation, we can predict how potential methods of intervention and incentives might change real-world behaviours.
Managers have been trying to manipulate employee motivation for decades with compensation-based safety programs, but these programs often create short-term gains and long-term losses as the system unravels due to the natural human desire to gain as much reward from as little work as possible. To accomplish behaviour modification, managers must first recognize that work is a social activity, meaning simple reward dynamics, when properly applied, can have drastic effects on the way people accomplish tasks. They respond to incentives, but in many cases, incentives are misplaced and don’t end up prioritizing the work behaviours they were created to modify.
In systems where employees are rewarded for meeting production goals, they will often cut corners and ignore safety procedure to accomplish tasks more quickly. This is because behaviour stems directly from the consequences of our action. In respect to safety, this means that if employees can expect increased rewards for meeting production goals by skipping safety procedures and experience infrequent incidents, most people will continue to cut corners. In drastic cases, workers may even avoid reporting incidents that have occurred if they believe reporting the incident will take away their reward.
So how do we remedy this misplaced motivation? Many managers may ask why they can’t just further incentivize safety goals with larger compensations. This bandage may temporarily bolster statistics, but incidents will likely soon bounce back as workers adapt to the new standard and once again find ways to further ‘optimize’ work efficiency by cutting corners, which destroys safety programs and productivity internally.
So how can management effectively engage in BBS? The simplest way to shift behaviour is to apply incentives to desired behaviours as opposed to results. This requires us to use the scientific process to dissect work habits to expose employee motivation and naturally realign incentives.
The Scientific Process
Keep organizational focus on safety culture and improvement will take root top-down, bottom-up, and throughout. These improvements in safety will help avoid the huge direct and indirect costs of incidents, and these increased behavioural efficiencies tend to also have a positive effect on production statistics and overall worker satisfaction.